Aluminum die-casting is a kind of forging, which is pouring molten or semi-molten metal material into the pressure chamber of an aluminum die-casting machine, and under the action of high pressure, it is filled in the aluminum die-casting die at a very high rate, and is It is a precision casting method that makes molten or semi-molten metal materials refrigerated and condensed under high pressure to obtain the benefits and efficiency of castings. The characteristics of the casting process are conducive to the design of castings to consider the regulations of the casting process. Let's take a look at the advantages and disadvantages of aluminum die casting.
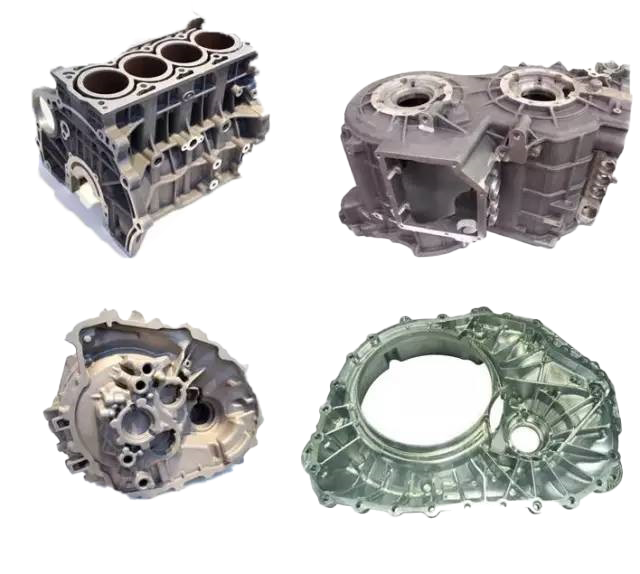
Advantages of Aluminum Die Casting
- High efficiency in manufacturing, and the processing process is very easy to complete mechanical automation and automation technology. Generally, the average value of cold chamber die-casting machine is 50-90 times per hour, while the average value of hot chamber die-casting machine is 400-900 times per hour, and the production efficiency is high.
- The specifications of castings are of high precision and high process performance. The general tolerance level of castings is IT13~IT15 in GB/T1800-2009, and the higher precision can achieve IT10~W11. The roughness gauge is 3.2~1.6 bucket m, and some parts reach 0.8 bucket m. Due to the high specification precision and high process performance of castings, castings that are not too high can be used immediately, preventing machining or less machining, which improves the utilization rate of aluminum alloys and saves a lot of money. Manufacturing cost of machining.
- The physical properties of castings are higher. The metal material melt has a faster cooling rate in the aluminum die-casting mold, and crystallizes under the working pressure, so the layer of crystals near the surface of the casting is thin and the structure is high-density. Compressive strength and strength are high.
- It can be aluminum die-casting complicated and thick-walled parts. Castings can have complex parts, and the thickness of the parts can be smaller. The small wall thickness of aluminum alloy castings is 0.5 mm, and the small wall thickness of zinc alloy die castings can be 0.2 mm.
- Casting parts that can be embedded with other raw materials. In this way, precious raw materials and production costs can be saved, and complex parts can be obtained and the characteristics of parts can be improved, reducing the amount of installation labor.
Defects of Aluminum Die Casting
- It is very easy to cause air holes in castings. Because the metal material melt fills the mold cavity at a very high rate during aluminum die-casting, and the mold material has no air permeability, the castings produced by the general aluminum die-casting method are very likely to cause blowholes. Because of the existence of air vents, the compressive strength of the casting cannot be improved according to the quenching and tempering treatment and its application at high temperature; in addition, the remaining amount of processing of the parts should not be too large, otherwise the hard bottom of the surface of the casting will be removed. The surface layer of the casting is exposed by the vent holes around the surface.
- Not suitable for small and large batch production. Aluminum die-casting molds are complicated and expensive, so they are generally only suitable for large-scale production.
- When aluminum die-casting high melting point aluminum alloy, the service life of the abrasive tool is relatively low. Some metal materials (such as alloy copper) have a high melting point, and the requirements for heat-resistant deformation and thermal fatigue limit of aluminum die-casting raw materials are very high, and the service life of abrasive tools is relatively low. At present, the raw materials of castings are mainly aluminum alloy profiles, zinc alloy materials and die-casting aluminum. Light metals are rarely produced and processed by aluminum die-casting.
Conclusion
If you are looking for a pressure die casting machine tonnage calculation,die casting machinery parts,oem die casting manufacturer, we hope we will be your best choice.